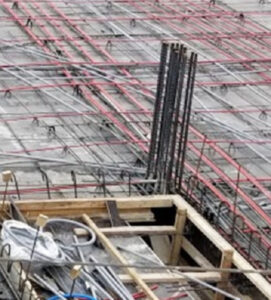
We’re busting all the most common myths that we see about post-tensioning to help you learn more about post-tensioned slabs and their uses.
We’ve been using the method of post-tensioning all the way since the 1950s. Today, it’s popular in all kinds of projects, including high-rise offices, residential buildings, and parking structures. You may be an architect trying to understand how to design spaces or an engineer who hasn’t learned enough about post-tensioning just yet. Thankfully, we have the scoop on everything you need to know. We’re busting all the most common myths that we see about post-tensioning to help you learn more about post-tensioned slabs and their uses.
Cutting Holes or Openings is Difficult
Like any other building method, you can make modifications to post-tensioned slabs—provided you consider this in the initial design. Designers can use tendon layouts which will allow for knockouts and openings. Some people may avoid post-tensioning, particularly in offices and hospitals, due to this misconception. However, these are some of the spaces that would benefit most from post-tensioned slabs if they only knew their potential.
Post-Tensioned Garages Are More Expensive
Remember that the budget of an entire structure is more inclusive than your initial construction costs. You may end up spending more upfront for post-tensioning in parking structures, but you are going to end up spending less on the back end when it comes to repair and maintenance costs. Precast is going to be more expensive during the entire lifecycle of a building.
Post-Tensioning Creates More Shortening
The truth is, any concrete you use will experience shortening. That’s just part of how concrete cures. It ends up changing in volume and most often, we see some shrinking. While contractors are able to control this to some degree by accounting for it from the get-go, it’s an inevitability. A post-tensioned slab will also experience elastic shortening but it’s an insignificant difference when compared to non-prestressed buildings.
Don’t Use Post-Tensioning in Below-Grade Work
Below-grade applications include anything like a parking garage that is built beneath a building. Some people falsely believe that there isn’t room to stress the post-tensioning in these situations due to the walls or because there may be cracking. However, experienced specialists know how to reduce cracking and maintain durability.
Always Use More Post-Tensioning
While we don’t want people to be scared off from post-tensioning due to myths that have gone around, it’s also not a fix for everything. Using post-tensioning won’t fix poor design practices. Adding more rebar to conventional concrete will almost always help, but post-tensioning is an active force on concrete—so if you have too much of it, you can cause severe issues like cracking, deflection problems, or even blowouts.
Concrete Visions Will Get The Job Done Right
Concrete Visions has been working with clients for over 25 years. Our G&M Services installers are certified with the industry’s major firestop product manufacturers. As part of our firestop service, we can assess abnormal field conditions and, with the manufacturer’s technical support assistance, provide engineering judgments in a timely fashion to comply with contract specifications. Our Field Mechanics undergo ongoing training, including mandatory monthly safety meetings, weekly Toolbox Talks where safety and equipment information is shred, and trainings on safe work standards and safety best practices.