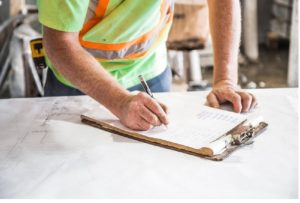
When you need core drilling for your construction project, you’ll likely want to turn to a professional.
When you need core drilling for your construction project, you’ll likely want to turn to a professional. Although drilling a core is something common to construction, it requires specific and expensive equipment that not all construction teams can afford, or need, to have on hand. Most organizations will subcontract a professional core driller, but it’s hard to know how to choose the right person. Core drilling can be complicated, and when not done correctly, it can lead to severe and expensive repairs. While there’s always the chance to look up reviews and Better Business Bureau reports, there are a few other factors you can look at as well.
What Equipment Do They Use?
The first question to ask any potential concrete core driller is what type of equipment they are using. Drilling through concrete is difficult and takes time – and if the equipment isn’t up to snuff, it can cause delays and even damage. A reputable company will have well maintained and high-quality tools that can get the job done on time. In general, they’ll be using a diamond drill bit and high powered drills, but quality tools are only as useful as their maintenance and care.
What Are Their Safety Protocol?
With the amount of risk that construction in general and core drilling, in particular, can bring, employing a team that takes safety seriously is of utmost importance. Having a preventable accident on your site is something that costs you money and time, not to mention the negative experience for the staff member. Before you hire a team, take a look at their safety plan and accident records. It will help to ask if they have any safety certifications as well.
What Kind Of Experience Do They Have?
When you’re drilling a concrete core, it must be precise and is a complicated procedure. You rarely have the time or ability to deal with mistakes or delays. This is why hiring a team with plenty of experience is critical. It will help to look for a company whose focus is concrete core drilling alone.
Concrete Visions Will Get The Job Done Right
Concrete Visions has been working with clients for over 25 years. Our G&M Services installers are certified with the industry’s major firestop product manufacturers. As part of our firestop service, we can assess abnormal field conditions and, with the manufacturer’s technical support assistance, provide engineering judgments in a timely fashion to comply with contract specifications. Our Field Mechanics undergo ongoing training, including mandatory monthly safety meetings, weekly Toolbox Talks where safety and equipment information is shred, and trainings on safe work standards and safety best practices.
Visit our website to see how we can be of service to you, and follow us on Facebook, Twitter, and Linkedin.