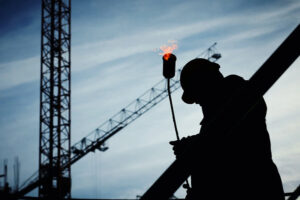
Today, we’ll be comparing wet core drilling with dry core drilling so you can figure out which will be better for your project.
Are you drilling holes inside of concrete structures? If so, you might want to use a core drill bit, especially if those holes have a diameter greater than two inches. Many variables have to be accounted when deciding which drill bit will be best suited for your situation. One debate you’ll face is whether you should do wet or dry core drilling. Today, we’ll be comparing wet core drilling with dry core drilling so you can figure out which will be better for your project.
Wet Core Drilling
For most drilling projects, wet core drilling is going to be the better option. Wet core drill bits use water to make it easier for drills to penetrate through concrete surfaces. Water allows drill bits to get through material more quickly and efficiently than other kinds of core bits would be able to accomplish.
In a similar manner to dry core drilling, which we will review later, wet core drill bits have centers that are hollow. This lets them take the core out of the hole and leave a clean surface behind.
Wet core drill bits have a multitude of applications, such as for manholes, masonry for pipes, or plumbing, among other things. Since wet drilling allows holes to be more sturdy, it’s often a better choice than dry drilling. Dust is also kept under better control when you use wet core drill bits instead of dry.
Dry Core Drilling
As the name implies, dry core drill bits are, well, dry. Like with wet drilling, dry core drill bits have centers that are hollow, which lets them extract cores from holes. Dry bits place greater stress on saw blades, meaning the speed of the drill isn’t quite as fast as wet drilling.
While wet drilling is more popular in many situations, it isn’t always the best choice for a project. There are purposes that are better served by dry drilling instead. For example, dry drilling is better whenever electrical wires are involved. It’s also the better option whenever you’re doing either soft brick or medium brick drilling.
Concrete Visions Will Get The Job Done Right
Concrete Visions has been working with clients for over 25 years. Our G&M Services installers are certified with the industry’s major firestop product manufacturers. As part of our firestop service, we can assess abnormal field conditions and, with the manufacturer’s technical support assistance, provide engineering judgments in a timely fashion to comply with contract specifications. Our Field Mechanics undergo ongoing training, including mandatory monthly safety meetings, weekly Toolbox Talks where safety and equipment information is shred, and trainings on safe work standards and safety best practices.