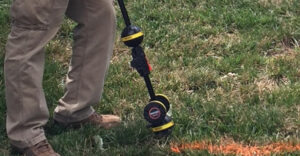
There’s actually more to rebar than most people realize, including different types, diameters, and sizes.
People who are familiar with concrete work know that most projects require some sort of reinforcement. Why – isn’t concrete incredibly sturdy? In short: concrete is incredible strong under compression but relatively weak in terms of tensile strength. So to resist cracking as it is bent or twisted, concrete has to be reinforced. In almost all cases this reinforcement comes in the form of rebar. But what is rebar? (Hint, it’s a portmanteau of reinforcing and bar.) There’s actually more to rebar than most people realize, including different types, diameters, and sizes.
Carbon Steel
Carbon steel rebar is the most universal type. It is appropriate to almost every size and type of project. The biggest drawback is that it corrodes and once it does it will expand and cause the concrete to crack. If it is possible that the rebar will be exposed to water saturation or humidity, it isn’t the best choice.
European
European rebar is an alloy made mostly of manganese. It is the most prone to bending, so it is not good for areas that experience earthquakes or for projects that will be subject to tensile pressure. It is usually the least expensive.
Epoxy-Coated
Black rebar that has an epoxy coating is up to 1700 times more resistant to corrosion. The coating itself is fragile, however, and can be chipped off if the rebar is handled roughly. The coating also adds some additional cost.
GFRP
GFRP, Glass Fiber Reinforced Polymer, is a composite similar to carbon fiber. It will not corrode at all but it also won’t allow for field bends. If you’re considering GFRP, make sure you’re comparing the price by linear foot. GFRP is extremely light so you get a lot more per pound of this than a pound of carbon steel (but the price per pound difference can be shocking).
Galvanized
Galvanizing is another process, like epoxy coating, that improved black rebar’s resistance to corrosion. It only increases the corrosion resistance by about 40 times, but it is much more durable than epoxy coating. However, it is also about 40% more expensive than epoxy-coated rebar.
Stainless Steel
Finally, stainless steel rebar is the most expensive, coming out usually 800 times more costly than epoxy-coated rebar. It is 1500 times more resistant to corrosion than black rebar, far more resistant to damage than epoxy or even galvanized rebar, can be bent in the field, and generally is overkill for most projects. With the exception of very specialized cases, the value of stainless steel rebar doesn’t justify the cost.
Concrete Visions Will Get The Job Done Right
Concrete Visions has been working with clients for over 25 years. Our G&M Services installers are certified with the industry’s major firestop product manufacturers. As part of our firestop service, we can assess abnormal field conditions and, with the manufacturer’s technical support assistance, provide engineering judgments in a timely fashion to comply with contract specifications. Our Field Mechanics undergo ongoing training, including mandatory monthly safety meetings, weekly Toolbox Talks where safety and equipment information is shred, and trainings on safe work standards and safety best practices.